Explore the importance of garage baseboard installation and maintenance because a well-installed baseboard can dramatically improve the longevity and aesthetic of your garage.
Key takeaways:
- Baseboards protect walls, improve aesthetics, and contribute to thermal efficiency.
- Choose baseboard materials based on moisture exposure and desired maintenance.
- Proper installation includes measuring, surface preparation, and securing the baseboards.
- Consider waterproofing measures and compatibility with garage flooring options.
- Baseboards provide insulation benefits and may require repair or replacement over time.
Purpose of Garage Baseboards
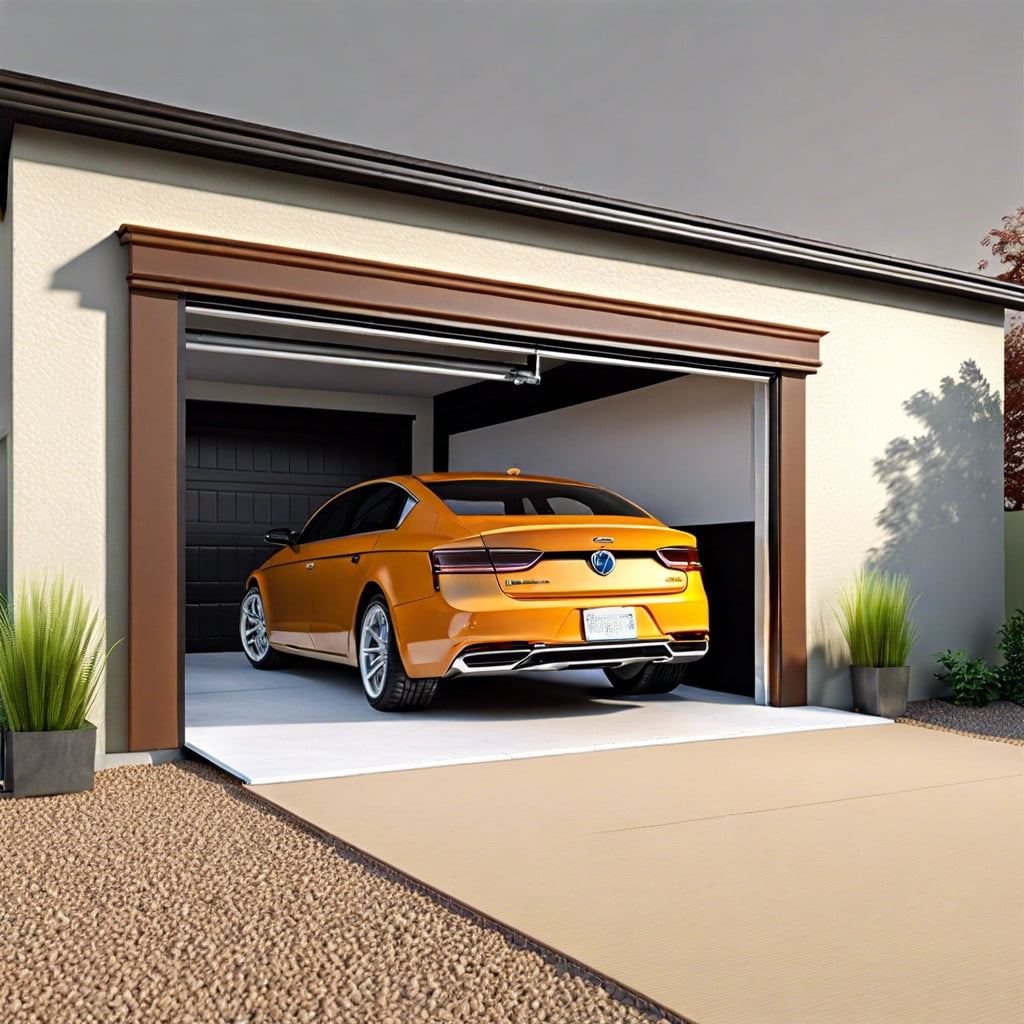
Baseboards serve several critical functions within a garage setting. Primarily, they protect the base of the walls from impacts, abrasions, and moisture, which can stem from activities typical in a garage, like moving tools or vehicles. This protective barrier helps to maintain the integrity of the wall material, potentially extending its longevity.
Moreover, baseboards provide a finished look, covering the junction where wall surfaces meet floors and hiding any uneven edges or gaps. This enhancement contributes not only to the overall aesthetics of the space but also prevents the accumulation of dust and pests by sealing off crevices.
Additionally, in climate-controlled garages, they can contribute to thermal efficiency by acting as an extra seal against drafts, helping to maintain consistent temperatures and potentially reducing energy costs.
Types of Garage Baseboards
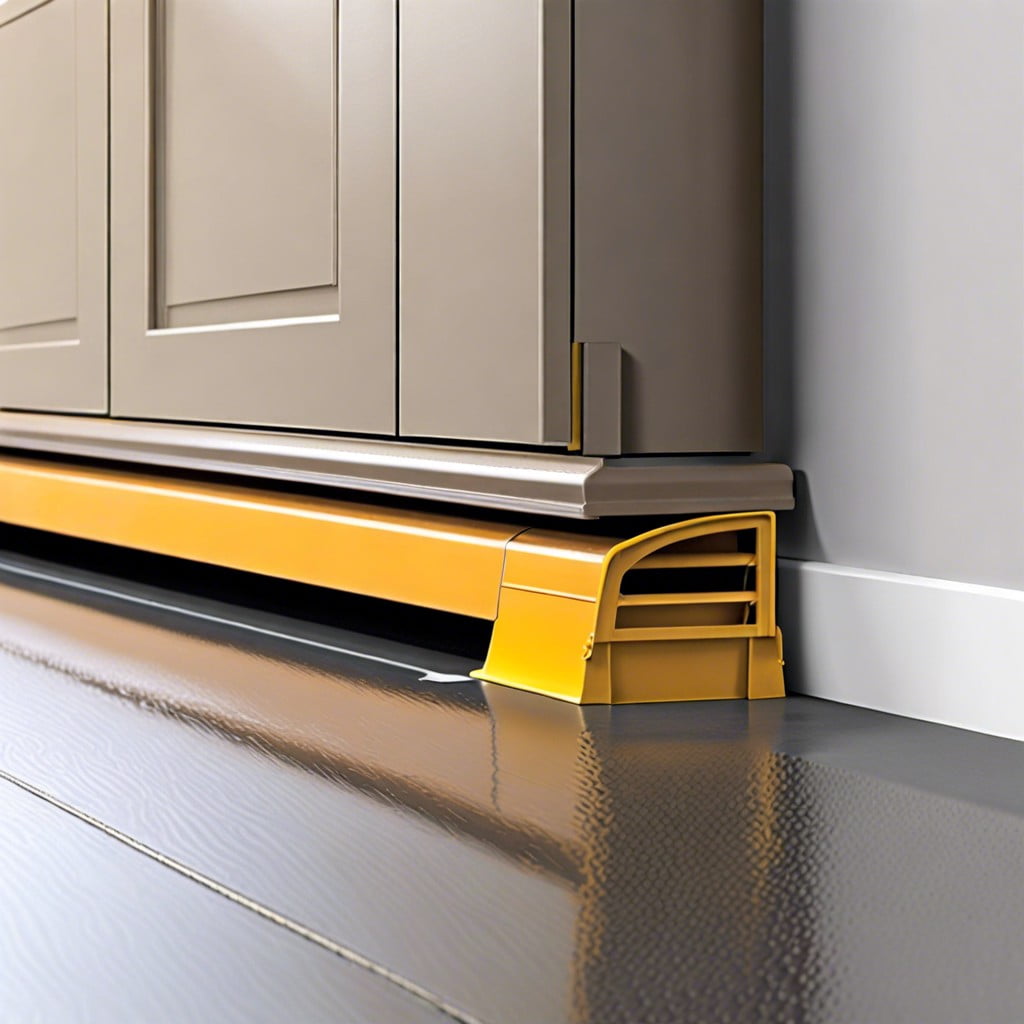
Selecting the right type is crucial to both the functionality and the aesthetics of your garage. Traditional wood baseboards offer a classic look and are readily available. They can be painted or stained to match your garage’s interior. However, they may not be the best choice for moisture-prone environments.
PVC or vinyl baseboards are increasingly popular due to their moisture resistance and durability. They require minimal maintenance and can withstand the rigors of a garage environment. Metal baseboards, such as aluminum or steel, provide an industrial look and are highly resistant to moisture and pests. These are ideal for a garage with heavy-duty activities.
MDF (Medium-Density Fiberboard) baseboards present a cost-effective solution with a smooth finish that emulates real wood. Polyurethane baseboards are another alternative, offering the look of wood without susceptibility to moisture or insects.
For those who need extra protection against dampness, rubber or plastic baseboards designed specifically for garages offer superior water resistance and are simple to clean. They may not have the range of styles found in other materials but are unmatched in practicality.
Each material brings its unique benefits and considerations. When choosing, contemplate your garage’s typical use, moisture exposure, and desired maintenance level.
Materials for Garage Baseboards
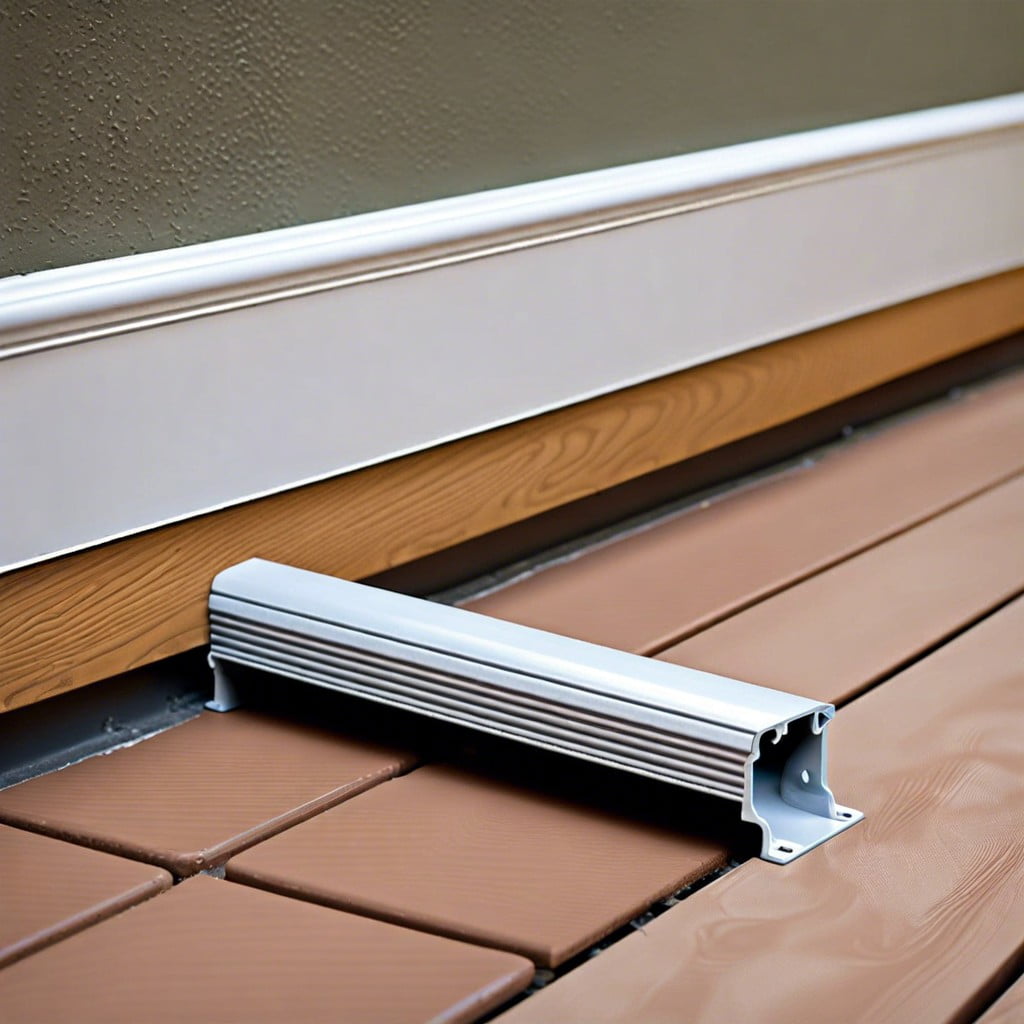
Selecting the right material for your garage baseboards is crucial for both aesthetics and durability. Wood, often used for its classic look, is an excellent choice for climate-controlled garages but may require more maintenance in high-moisture environments. MDF, a more affordable wood alternative, offers a smooth finish for painting but can swell and deteriorate if exposed to water.
PVC baseboards emerge as a winner for garage environments because of their resistant nature. PVC is impervious to water and insect damage, making it particularly suited for garages that may experience damp conditions or are prone to pests.
Metal baseboards, such as aluminum or steel, provide a modern look and boast remarkable longevity. They are not affected by moisture and can withstand the wear and tear of garage activity, including accidental bumps from cars or tools.
Considering factors such as exposure to moisture, potential for impact damage, and the desired aesthetic can guide homeowners to the best material choice for a functional and visually pleasing garage baseboard.
Installation of Garage Baseboards
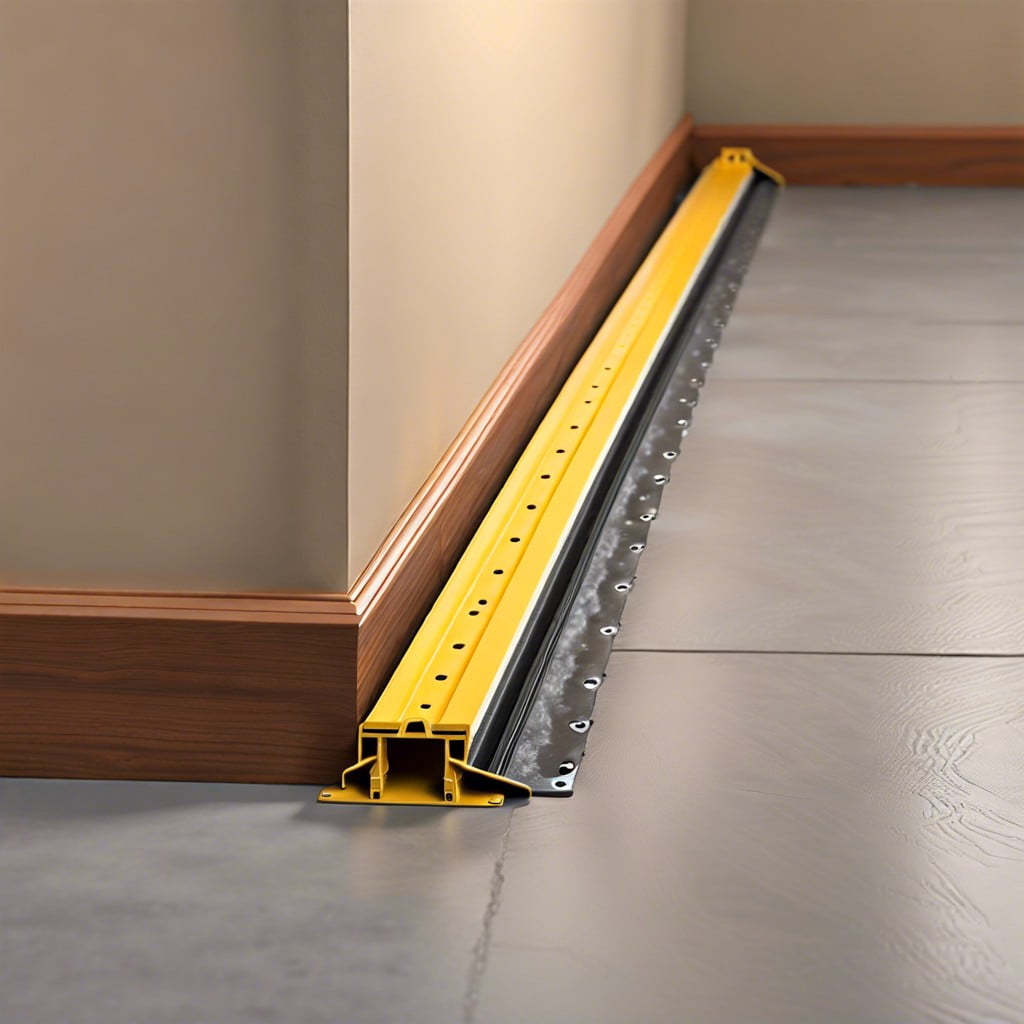
Proper installation is critical to ensure garage baseboards perform effectively. Here’s a concise look at the installation process:
1. Measure and Cut: Measure the garage perimeter to determine the length of baseboard needed. Use a saw to cut baseboard material to the required lengths, factoring in corners and doorways.
2. Surface Preparation: Clean the bottom portion of the wall where the baseboard will be attached. Ensure it’s free from dirt, grease, and debris for a secure fit.
3. Mark and Level: Use a chalk line or level to mark where the top of the baseboard will sit, ensuring a straight, level line all around the garage for uniform installation.
4. Adhesive Application (if applicable): Apply construction adhesive to the back of the baseboard for added durability, especially in garages where moisture is a concern.
5. Securing the Baseboards: Nail or screw the baseboard into place at stud locations, which typically are every 16 or 24 inches along the wall. For masonry walls, use appropriate masonry anchors.
6. Caulking and Sealing: To prevent moisture penetration, caulk the top and bottom edges of the baseboards. This seals the baseboard to the wall and floor.
7. Finishing Touches: Fill any nail or screw holes with wood filler (for wooden baseboards) or caulk, then sand the area smooth once it’s dry. If desired, finish with paint to match or complement garage walls.
By following these steps, you can ensure that your garage baseboards are installed for maximum protection and aesthetic appeal.
Waterproofing Considerations for Garage Baseboards
Selecting moisture-resistant materials is crucial, as garages are prone to dampness and water exposure which can cause mold and material deterioration. PVC or vinyl baseboards offer excellent water resistance and are less susceptible to moisture-related damage compared to wood.
Raising baseboards slightly off the floor prevents direct contact with water when the garage floods, ensuring the longevity of the installation.
Sealants can be applied to baseboard joints and where the baseboards meet the floors and walls, providing an additional layer of protection against water intrusion.
Proper garage drainage should be maintained to reduce the risk of standing water that can adversely affect baseboards.
In climates with high humidity or frequent exposure to water, consider installing concrete baseboards, which are inherently waterproof and resilient against such conditions.
Cost Considerations for Baseboard Materials and Installation
When budgeting for garage baseboards, several factors influence the total cost:
1. Material Choice: Baseboard prices vary by material. Wood and MDF are generally more affordable, PVC and vinyl offer mid-range options, while aluminum or stainless steel could be considered premium choices due to their durability and resistance to damage.
2. Length and Thickness: The amount of baseboard needed correlates with perimeter length of the garage. Thicker, more decorative baseboards also cost more than simpler, thinner options.
3. Labor Costs: Depending on your location and the complexity of the job, installation costs can differ. DIY installation can save money, but consider the value of a professional’s skill and efficiency for optimal results.
4. Prep Work: The state of your garage walls can affect costs. If wall repair or prep work such as sanding or priming is needed, expect additional expenses.
5. Corner and Trim Pieces: Corners and special trim pieces can add to the overall cost, as these unique cuts may require more precise work and extra materials.
6. Sealant and Adhesives: For a finished look and added durability, factor in the cost of caulking, sealants, and adhesives, especially in garages exposed to fluctuating temperatures and moisture.
Assessing these points helps in creating a realistic budget that aligns with your design preferences and garage needs.
DIY Vs. Professional Installation
Deciding between DIY and professional installation hinges on several factors:
Skill Level: Installing baseboards is a manageable task for those with moderate carpentry skills. It includes cutting, measuring, and the use of basic tools like a saw, hammer, or nail gun.
Time Commitment: DIY projects require a time investment. Evaluate if you can allocate sufficient time to complete the work without rushing, as this might affect the quality.
Tools: Access to the right tools is essential. You’ll need a miter saw for precise cuts, a nail gun or hammer for secure attachment, and possibly caulking tools for sealing.
Complexity of Design: If your garage has numerous corners or you desire custom baseboard profiles, the complexity increases. These scenarios might benefit from a professional’s expertise.
Budget: While DIY can reduce labor costs, mistakes can be costly. Professionals factor in the cost of materials and labor, which can provide value through expertise and efficiency.
Warranty and Liability: Professional installations often come with a warranty. Any mistakes made by a contractor are typically their responsibility to fix, providing peace of mind.
Consider these points to ensure a successful project, whether you choose to tackle the installation yourself or hire a professional.
Compatibility With Garage Flooring Options
When selecting baseboards for your garage, considering the type of flooring can make a significant difference in both aesthetics and function. If your garage floor is coated with epoxy, for example, smooth baseboard materials like PVC or vinyl are advisable as they create a seamless transition and are easy to clean.
For concrete floors, a more rugged baseboard material such as wood or metal might be preferred for its durability against potential dings or scrapes.
Interlocking garage floor tiles present a unique challenge; the baseboards should accommodate the tiles’ expansion and contraction with temperature changes. Flexible baseboard options can accommodate these movements without cracking or becoming detached.
Carpeted garages, although less common, require baseboards that can withstand potential moisture buildup without warping or rotting. In this situation, treated woods or moisture-resistant composites ensure longevity.
It’s essential to match the height of the baseboards with the thickness of the flooring material. Taller baseboards may be required for thicker, cushioned garage floor coverings to ensure adequate protection and visual proportion.
For garage floors that experience frequent spillages, such as oils or other chemicals, non-absorbent baseboard materials will make for easier cleanup and maintenance. Metal or plastic materials are best for these environments.
By matching your baseboards to your garage flooring, you’ll ensure a functional, cohesive, and finished look that complements your garage’s design and usage.
Insulation Benefits of Proper Baseboard Installation
Installing baseboards in your garage isn’t just about aesthetics—there’s a practical side too, especially when it comes to insulation. When properly installed, baseboards create a seal at the bottom of the walls, reducing the draftiness that can plague many garages. Here’s how they make a difference:
- Airflow Reduction: By sealing the gap between the wall and the floor, baseboards minimize the intrusion of cold air, keeping the garage warmer during cooler months.
- Energy Efficiency: A well-insulated garage means less heat escapes, which can translate to lower heating bills if your garage is climate-controlled.
- Pest Deterrent: Baseboards can deter pests by closing off the small openings that might otherwise be an entry point for insects and rodents.
- Moisture Control: A proper seal can also prevent moisture from seeping in, which is crucial for preventing mold growth and protecting stored items.
- Enhanced Durability: Insulated garages with temperature moderation can reduce the strain on vehicles and equipment, as consistent temperatures are generally better for storage.
By focusing on the seal and material quality of your baseboards, you contribute significantly to the overall insulation of your garage space.
Repair and Replacement of Garage Baseboards
Regular inspection for signs of damage such as warping, cracking, or rot is crucial in maintaining the integrity of garage baseboards. When damage is spotted, timely repair or replacement helps prevent moisture penetration and structural issues.
For minor damages, fillers or sealants can be used to restore the baseboard’s appearance and functionality. Replacement, however, is necessary when extensive damage compromises the baseboard’s ability to protect against pests and moisture. Remove the affected section carefully to avoid damage to the wall or the floor.
Installation of the new section should match the existing baseboard profile for a uniform look. Consider using materials like PVC or vinyl for areas with high moisture exposure, ensuring long-term durability. When working with wooden baseboards, it’s advisable to treat the replacement section with water-resistant paint or sealant before installation.
Always ensure that the fit is snug, and the sealant is properly applied to avoid future issues.
FAQ
What kind of baseboard to use in a garage?
For a garage, vinyl baseboard is an excellent choice due to its high traffic durability, scratch, and stain resistance.
Should I put baseboard in garage?
Yes, installing baseboards in your garage is beneficial as they serve the crucial role of protecting the interior from water damage and other potential threats.
What baseboards are in style for 2023?
The Eased Edge Baseboard, with its modern and simple design, is in style for 2023.
How does the installation process of baseboards in a garage differ from that in other parts of the house?
The installation process of baseboards in a garage typically requires more durable materials due to higher exposure to moisture and temperature variations, compared to other parts of the house that have more controlled environments.
What materials should be avoided when choosing baseboards for a garage?
Materials like particle board and MDF should be avoided when choosing baseboards for a garage due to their susceptibility to moisture and damage.
How can baseboards enhance the overall aesthetic of my garage?
Baseboards can enhance the overall aesthetic of your garage by providing a clean and finished transition between the walls and the floor, concealing any gaps, and complementing the architectural style of your garage.